Welcome back to another blog. Nothing too exciting has happened to me in the last couple weeks. Been just hanging out and really trying my best to improve myself in the gym before I head back to school. I have also started getting some things organized so I’m not frantically packing in the last draining moments before I pack up the car to move to Edmonton.
I’m going to give you guys a bit of a tour of Alberta Newsprint Company (ANC) from a process stand point.
First is where we get our wood from. ANC gets all their wood from other mills in the area who truck their leftover wood chips to us. They get brought into our yard and transported to the chip pad. When the trucks get emptied, they go onto a large platform that lifts them nearly vertical and dumps out all the wood chips.

We are constantly replanting trees to revitalize the forest, thus allowing us to continue operating without damaging the environment.From the chip pad, the wood chips are transported on large conveyors into the mill. These conveyors move very quickly and move large quantities of wood chips at a time.
From the chip pad, the wood chips are transported on large conveyors into the mill. These conveyors move very quickly and move large quantities of wood chips at a time.

Next, the wood chips enter our pulp mill, which is the first half of the whole facility. The wood chips go through a series of mixing and thickening processes to turn the chips into a thick, white pulp. Specific chemicals are added to the pulp allowing it to stick together easier and become the correct shade of white. There is a lot of variation and testing that allows the technical department to optimize the mixture of pulp. The pulp is put through many further filters and refiners to create the cleanest pulp possible.

After the pulp is made, it is pumped onto the paper machine. The paper machine’s main goal is to take the thick pulp and extract as much water out of it as possible. There are a series of large rolls and felts(almost like a really wide series of pulleys and drive belts) that squeeze and compress the pulp, removing large amounts of water and moisture. The paper machine runs at approximately 1500 meters per minute (90 km/h), which allows a lot of paper to be made in a day.
These felts that the paper rides on wears down over time, so a few times per year the operators replaces the fabric. Worn down felts are not good to use since they directly affect the quality of the paper.

Once it is through all 4 “presses” it moves into the dryer. The dryer (as you can probably guess) dries out the paper. It is upwards up 40°C in there, so we have to be very careful when in that area. The dryer section consists of many felts and rolls again, stretching down the operating floor. It uses a mixture of heat and compression to get rid of more water, but by this time, most of the water would have been removed by the paper machine.

When the paper reaches the end of the dryers, it begins moving through the calendar stack, which is the last opportunity to perfect the paper quality before it is made. This part of the machine can adjust the texture and gloss of the paper. Skilled operators are trained to know exactly how to alter this part of the machine to achieve the quality required.

Next comes the reel spool. The paper sheet wraps around a rubber coated roll and in 45-60 minute increments, the roll fills up to its maximum diameter (roughly 10 feet). At this point, the operators use specialized automated air tools to cut and blow the paper sheet onto a new rollin a split second. The machine does not slow down for this, so the sheet is still moving along at 1500 meters per minute. This takes the utmost amount of precision to prevent the sheet from breaking and jamming while doing this transfer process.

Operators transport the large roll down a series of pneumatic stoppers and bring it into the winder. The winder is a specialized, computer controlled piece of equipment that cuts the paper to specific widths and rolls it onto individual cardboard cores. The width and diameter of these smaller rolls vary by customer. Customers will take these rolls and put them into their printing machines to make newspapers, magazines, burger wraps, and many more paper products.

The paper is loaded onto a series of conveyors that take each small individual roll down an elevator. This goes into our warehouse, which hosts most of our stocked paper and the wrap-line. The wrap-line wraps the paper in cardboard to prevent it from being damaged during shipping. These wrapped rolls are either stored in the warehouse or shipped out via rail, truck, or boat.

Alberta Newsprint Company also hosts a very efficient and effluent treatment facility that clarifies used mill water and sludge, turning it into a clean water that can be given back to the river. Specific biological oxygen demand (BOD) levels are required to put water back into the river, so it takes a lot of precision to meet these requirements.
There are many other side businesses involved with AlbertaNewsprint Company including material trans-loading, power creation, and logging.
That’s probably a lot for you all to take in but I hope you enjoyed the mini tour here and all the pictures to go along with it. The mill has a lot of parts of the process that even I don’t fully understand, butI always find it interesting to learn more.
See y’all next time.
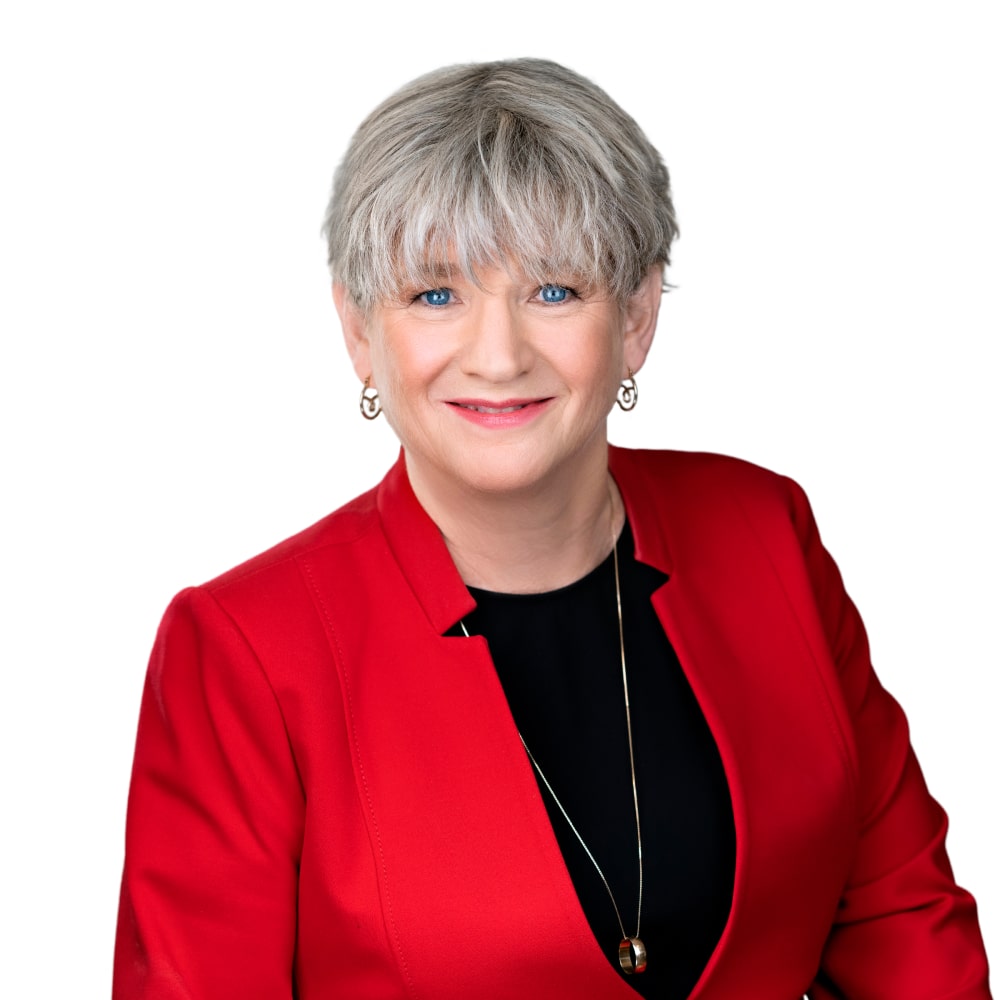